Funktion und Chemie des Gaserzeugers
Ursprünglich sind die mobilen Gaserzeuger für die Verwendung von Holzkohle konstruiert worden. Auf Drängen von Frankreich wurden die Entwicklung der Holzvergaser forciert (siehe unter Georges Imbert). In Deutschland gab es wegen dem kriegsbedingten Benzinmangel die meisten Gaserzeuger. Der am besten verfügbare heimische Treibstoff war und ist Braunkohle, die jüngste fossile Phase von Holz (Holz - Torf - Braunkohle - Steinkohle - Anthrazit). Während dem zweiten Weltkrieg wurden die meisten Gaserzeuger daher mit Braunkohle betrieben.
Während in der Schweiz hauptsächlich Holz und Torf verwendet wurde, war in Frankreich Holzkohle weit verbreitet. In Deutschland hingegen war Holzkohle wertvoll und rar. Deswegen wurde in der Landwirtschaft Holz vorgeschrieben, ansonsten war Braunkohle weit verbreitet. Je nach Verfügbarkeit wurde auch Anthrazit und Schwelkoks in speziellen Generatortypen vergast.
Sogenannt absteigende Vergaser können mit den drei bituminösen Brennstoffen Holz, Torf und Braunkohle betrieben werden (auf die verschiedenen Typen für aufsteigende bzw. Querstromvergasung für Anthrazit, Schwelkoks sowie für Holzkohle wird später eingegangen). Alle absteigenden Vergasertypen sind volkstümlich bekannt unter dem Begriff Holzgasgenerator.
Die Anlage am Opel Kadett ist ein Wisco Braunkohle Vergaser (DE), welcher auch mit Torf oder Holz betrieben werden kann.
Die Anlage am Ford Model A ist ein Kaiser Holzvergaser (CH), welcher auch mit Torf oder Braunkohle betrieben werden kann.
Zur Erklärung der Vorgänge im Gaserzeuger greife ich auf die Imbert- Anlage zurück. Diese ist historisch am besten dokumentiert und sie kann als Vorbild aller späteren Gaserzeuger bezeichnet werden. Viele Varianten wurden unter Umgehung der Imbert- Patente entwickelt. In Deutschland wurden Gaserzeuger-Patente während dem zweiten Weltkrieg annulliert. Man zwang die verschiedenen Hersteller zur Fabrikation von einheitlichen Gasgeneratoren.
Der Fahrzeug- Gaserzeuger ist eine Sauggas- Anlage, weil der Motor die erforderliche Gasmenge ansaugt. Zu Beginn übernimmt ein Ventilator die Funktion des Motors und saugt Luft durch das gesamte System. Am Eintrittsloch vom Gaserzeuger wird eine brennende Lunte hingehalten, die Sogwirkung zieht die Flamme in den Herd und facht dadurch den Generator an.
Nach 7 bis 15 Minuten kann das Gas am Ventilatoraustritt angezündet werden. Sitzt die Flamme ruhig auf dem Austrittsrohr und brennt rötlichblau und gleichmässig, so wird der Ventilator ausgeschaltet und das Ventil geschlossen. Unter Betätigung des Anlassers wird die Luftdrosselklappe langsam geöffnet, bis ein zündfähiges Gasgemisch entsteht und der Motor startet.
Manchmal wird das Gas kurz nach dem Anlassen schlechter. Dieses sogenannte Gasloch wird mittels Vollgas und weniger geöffneter Luftklappe überwunden, anschliessend ist das Fahrzeug betriebsbereit. Wenn der Motor in diesem Moment stoppt, so muss zuerst einige Minuten ventiliert und danach der Anlassvorgang wiederholt werden.
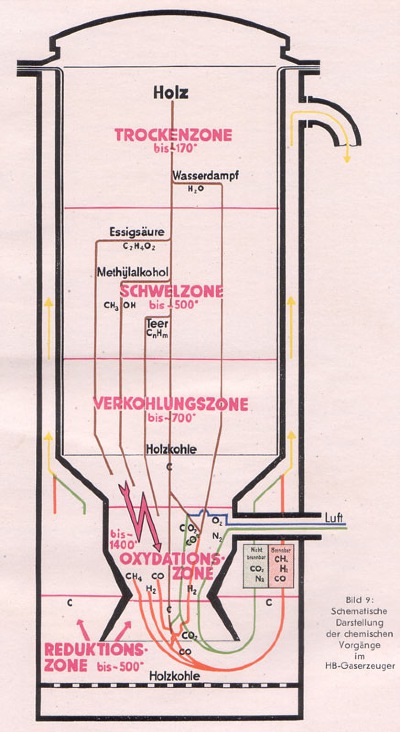
Schematische Darstellung
Die eintretende Luft verteilt sich durch Düsen in den Herd. In der Nähe der Düsen, d.h. in der Oxidationszone vergast die vorher entzündete Holzkohle mit der eintretenden Luft. Es entsteht einerseits brennbares Kohlenmonoxid CO. Andererseits entsteht auch unbrennbares Kohlendioxid CO2. Das CO2 wird in der glühenden Holzkohle unterhalb des Herdes zu Kohlenmonoxid CO reduziert. Über den Deckel des Generators kann Brennstoff nachgefüllt werden.
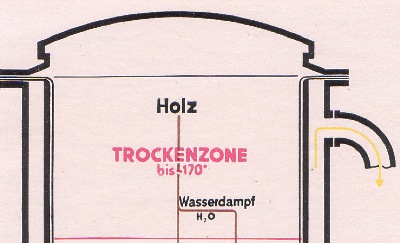

Ein Teil der Holzkohle fällt unverbrannt durch den Herd und bildet die sogenannte Reduktionszone.
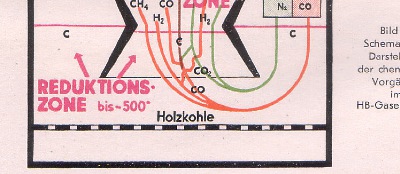
Oxidation
C + O2 = CO2 (Wärme erzeugend)
Wasserstoffbildung
CO + H2O = CO2 + H2 (leicht Wärme erzeugend)
C + H2O = CO + H2 (Wärme verbrauchend)
Reduktion
CO2 + C = CO + CO (Wärme verbrauchend)
Die Zusammensetzung des Gases ist durchschnittlich wie folgt:
Kohlenmonoxid CO 23%
Wasserstoff H2 18%
Methan CH4 2-4%
Kohlendioxid CO2 10%
Stickstoff N2 47%
Der untere Heizwert beträgt 1200 - 1400 kcal/m³ (5000-5800 kJ/m³). Der Luftbedarf zur Verbrennung im Motor ist etwa 1.0 - 1.2. Somit ist der Gemischheizwert ca. 600-650 kcal/m³ (2500-2700 kJ/m³). Der Leistungsabfall gegenüber Benzin (ca. 900 kcal/m³) beträgt daher 28-35%. Ein weiterer Leistungsabfall kann sich durch den geringeren Füllungsgrad des Motors ergeben (Strömungswiderstand im Generator) sowie durch die langsame Verbrennung des Generatorgases im Vergleich zu Benzingas.
Als Gegenmassnahme wurden die Motoren höher verdichtet oder aufgeladen, ausserdem erfolgte die Zündung 10-15° früher, meist manuell nach Gefühl. Zudem verfügten die meisten Anlagen über Manometer, sodass bei beginnender Verstopfung der Filter oder des Herdes rechtzeitig reagiert werden konnte. Aufgrund der Eigenheiten von Holzgas ergibt sich der wirtschaftlichste Betrieb mit einem grossvolumigen, langsam laufenden Benzinmotor (siehe Ford Model A mit Holzvergaser).
1 Liter Benzin entspricht:
ca. 2.5 - 3.0 kg Hartholz
ca. 3.0 - 3.5 kg Torf (Vorstadium von fossiler Kohle)
ca. 1.5 - 2.0 kg Braunkohle (auch bekannt als Unionbriketts)